Electric Signs
An Icon’s Second Act
Published
14 years agoon
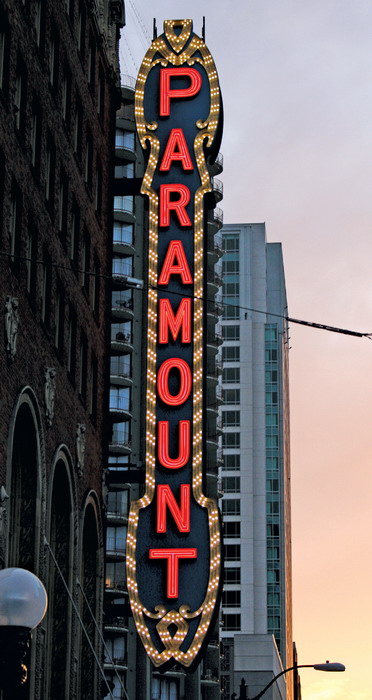
Ken Naasz is the design and development VP for The Sign Factory (Kirkland, WA).
In 1928, the worlds first TV station opened in New York; Mickey Mouse made his big- screen debut in Steamboat Willie; and Seattle’s most opulent theatre palace opened to the wide-eyed public with a landmark sign that featured 1,944 flashing bulbs and 5-ft.-tall, neon, open-pan channel letters. As part of the city skyline for more than 80 years, it has been deemed “the most significant sign in Seattle” by Seattle’s Landmarks Preservation Board. The original theatre and sign were designed by the famed Chicago architectural firm Rapp and Rapp. Originally built and installed in 1928, the sign was changed in 1930 to reflect its new name, the Paramount Theatre.
In December 2008, David Allen, director of operations for Seattle Theatre Group (owners of the sign), decided the old sign needed replacement after having endured many years of wet Northwest weather. Rust and decay had deteriorated its sheetmetal beyond repair. Birds and rodents ate away the old electrical wiring, which created a fire hazard. Pieces of the sign had begun falling off the marquee, which threatened the safety of pedestrians on the sidewalk below.
The Sign Factory (TSF), Kirkland, WA, contracted to remove the old sign and replace it with an exact replica. TSF’s field manager, Tom Bonifant, maintained the old Paramount sign for more than 15 years. Bonifant had spent more than a decade replacing its transformers, wiring, sockets and sheetmetal, so Allen entrusted him to manage the sign’s replacement.
Advertisement
Something old, something new
We began by surveying the existing sign for salvageable, original elements. We hired West Coast Structural Engineering Inc. (Mukilteo, WA) to analyze the steel and provide a structural observation and assessment report. Their analysis found the 12 x 5-in., steel I-beams and connecting, 15-in. C-channels in excellent shape, with only some surface rust in places. Not bad for projecting out the side of a building amidst often rainy environs for more than 80 years. However, the welded, 2-in., angle iron that connected the sign sections to the structure required replacement.
Next, Allen, Jim Risher, Jim Minar (TSF’s president and permit technician, respectively) and I met with Seattle’s Landmarks Preservation Board and provided the engineering data and preliminary designs. The submittal process entailed attending several to Architectural Review Committee meetings, drawing revisions and providing additional information to the committee.
The board approved the sign, with the stipulation that it match the original’s design and size. TSF built a full-scale, section prototype of the sign so board members could see and touch the actual paint colors, materials, neon tubes and LED bulbs. After having acquired a certificate of approval from the Board, we obtained sign and electrical permits from the City of Seattle.
Hatching the plan
AdvertisementWith approvals in hand, TSF began the manufacturing process. First, we made “dirty handprint” patterns onsite by placing large sheets of paper over the sign’s face and rubbing the paper to create a relief image. This allowed TSF to recreate the intricate scroll patterns and distinctive design elements with exacting detail.
In addition to making patterns, we took measurements from all sections to ensure accuracy. Next, we began the painstaking process of transposing the pattern and measurement information into our CAD/CAM computer system. On our design-station computer, which operates Windows XP Pro, a 2.67MHz Intel Core Duo processor with 2 GB of RAM, Corel X3, and Gerber’s Omega Composer version 3.6, we digitized the size and shape.
With the digital image saved, we downloaded the vector EPS files directly to our AXYZ 5010 dual-head, 6 x 10-ft., flatbed CNC router. We used Artcam Express 2009 and AXYZ Toolpath for Windows software to convert the files from EPS to NC format. The Sign Factory’s production manager, Shawn Spencer, managed the entire manufacturing process.
The signfaces measured 65 ft. tall overall and varied in width from 5 ft. 4 in. to 8 ft. 8 in., while each face was built in three separate sections for transport and installation ease. We routed the signfaces from 0.125-in. aluminum with the bulb socket holes and letter centers cut from the face. We cut grooves at a 0.031-in. depth to allow for insetting and welding of 3-in. x 0.063-in., chasing bulb channels.
The Seattle Theatre Group wanted the new sign be as "green" as possible. The 6 x 10-ft., aluminum sheets contain 17% post-consumer and 27% post-industrial, recycled content. Ryerson Aluminum provided the recycled sheetstock.
Heavy-duty signmaking
On the reverse side of the signfaces, we used a Miller Millermatic 275 220V, wire-feed welder to attach a 5-in.-wide, aluminum C-channel frame. TSF built 2 x 2 x 3/16-in., steel angle, custom rolling dollies to better access each section of the sign throughout the construction process. We designed the dollies with a rotisserie feature that allowed production crews to easily reach every sign section. This allowed TSF to save time and money and reduce the risk of damage to the signs during the construction process.
We welded aluminum channels from 0.063-in. material to the face sections using the grooves previously routed into the face. The open pan channel letters, which read “Paramount,” were wrapped with 0.080-in. aluminum. The letters were constructed with an 8-in. return to match the original letters.
Next, we primed the sign faces were with Akzo’s Grip-Gard Washprimer, a two-part, self-etching primer. Then, 1,944 UL-listed 660W/250V Suprolux Bakelite housing bulb sockets were installed into each hole routed from the face. We inserted router-cut, rigid foam insulation, which we coated with waterbased primer, into each socket to prevent overspray contaminating the sockets.
We painted the bulb channels and open-pan channel letters gold to match the existing sign. TSF also paid careful attention to the exact color to replicate the original sign’s patina. We sprayed on satin-finish, Matthews acrylic polyurethane paint. We then masked the gold areas and painted the signface blue to match the old paint color.
Following the painting process, we wired the bulb sockets with four colors of 1000V, 14-gauge wire. We then wired Rocox solid-state, four-way flashers to the sockets to provide the chasing action, which matched the original bulbs. To match the original bulb chasing action, we’d recorded the speed and action of the original bulbs. We replaced the original, 11W incandescent bulbs with HiteQ 0.75W LED lamps with frosted lenses that closely matched the originals.
Throughout the face construction, painting and wiring processes, we routed the 0.090-in.-thick aluminum back sections on our AXYZ CNC router. Access panels were strategically placed throughout the back of the sign to provide for service of the electrical components while avoiding the internal and external structure. Hinged covers were included on the panels to keep out the weather, birds and other critters. We welded the 0.080-in., aluminum sign returns to the back and face sections, and then primed and painted the sign back and returns to match the original color.
Every piece in place
Final assembly required installation of double-tube, 15mm, 30mA, clear, red-neon tubing within the open-pan channel letters. Single-tube, 15mm, 30mA, clear, pumped-blue neon completes the center tube within each letter. Using one transformer per letter, we installed VENTEX Gen III self-adjusting, UL 2161-listed, 120V/1.8 amp, ground-fault transformers to power the neon components. All told, the neon spans 420 linear ft.
Over two days – October 6 and 7 of last year – we removed the original sign and installation of the new sign sections occurred. We cut the old sign into five sections per side for removal. TSF estimated the sheetmetal’s weight at roughly 12,000 lbs., and the new sign’s aluminum weighed 6,000 lbs. The Sign Factory hired Apex Steel Inc. (Redmond, WA) to remove the old sign and complete all onsite welding. City inspectors performed a very detailed and comprehensive inspection of all the field welds.
Ness Cranes of Seattle provided a 40-ton crane with a 130-ft. lift. We also used a 125-ft. Genie lift throughout the removal and installation process. TSF’s 24-ft. flatbed truck, two 24-ft., flatbed trailers and 80-ft. Dyna-Lift crane truck transported the sign sections.
Thanks to Tom Bonifant and his crews, the installation progressed like clockwork and ahead of schedule. On October 21, a lighting ceremony was held, and the public got their first look at the bright, new sign. The response was overwhelmingly positive, and Seattle Theatre Group was thrilled with their beautiful new sign.
In addition to its aesthetic appeal, the sign will consume 90% less energy and save approximately 493,268kwh of electricity per year versus the old sign. That’s enough energy to power roughly 55 Seattle homes. The Paramount Theatre’s lighting upgrade and sign project also qualified the Seattle Theatre Group for approximately $56,000 in energy-efficiency rebates from Seattle City Light.
The Sign Factory is proud to have been a part of such an historically significant project. The Paramount Theatre’s sign will continue to shine brightly and illuminate the Seattle skyline for another 80 years (or more).
Equipment and Materials
Coatings: Grip-Gard® two-part, self-etching primer, from Akzo Nobel Coatings (Norcross, GA), (770) 662-8464 or www.signfinishes.com; satin-finish, acrylic-polyurethane paint, from Matthews (Delaware, OH), (800) 323-6593 or https://corporateportal.ppg.com/na/refinish/matthews
Cranes: Dyna-Lift 80-ft. crane, from Dyna-Lift Inc. (Clearwater, FL), (800) 200-0898 or www.dyna-lift.com; Genie 125-ft. lift, from Genie Industries (Redmond, WA), (800) 536-1800 or www.genielift.com; 40-ton crane, from Ness Cranes (Seattle), (888) 784-1054 or www.nesscranes.com
LEDs/Lighting: Solid-state, four-way flashers, from Rocox (Amarillo, TX), (806) 662-3800 or www.rocoxinc.com; Bakelite housing-bulb sockets, from Supro Lux (Irvine, CA), (949) 261-9924; 0.75W frosted-lens, LED bulbs, from HiteQ (City of Industry, CA), (866) 944-4837 or www.hiteqelectric.com
Metal: Recycled-content aluminum sheet, from Ryerson Aluminum (Chicago), (773) 762-2121 or www.ryerson.com
Neon: Single- and double-tube, 15mm, 30mA neon, from EGL (Berkeley Heights, NJ), (908) 508-1111 or www.egl-neon.com; Nine, ground-fault, 120V/1.8A Gen III transformers, from Ventex (Jupiter, FL), (800) 510-5400 or www.ventextech.com; #300 neon glass housings, from S & F Supplies (Brooklyn, NY), (800) 246-8233 or www.sfsupplies.com
Router: AXYZ 5010 dual-head, 6 x 10-ft., flatbed router, from AXYZ Automation Inc. (Burlington, ON, Canada), (800) 361-3408 or www.axyz.com
Software: AXYZ Toolpath for Windows, from AXYZ Automation Inc.; Artcam Express 2009, from Delcam Inc. (Windsor, ON, Canada), (877) 335-2661 or www.artcam.com; Omega Composer 3.6, from Gerber Scientific Products Inc. (South Windsor, CT), (800) 222-7446 or www.gspinc.com
Welder: Millermatic 175 220V wire-feed welder, from Miller Weldmaster Corp. (Navarre, OH), (330) 833-6739; www.weldmaster.com

SPONSORED VIDEO
Introducing the Sign Industry Podcast
The Sign Industry Podcast is a platform for every sign person out there — from the old-timers who bent neon and hand-lettered boats to those venturing into new technologies — we want to get their stories out for everyone to hear. Come join us and listen to stories, learn tricks or techniques, and get insights of what’s to come. We are the world’s second oldest profession. The folks who started the world’s oldest profession needed a sign.
You may like

NUtec Digital Ink Invests in Solar Energy for Facility

5 Reasons to Sell a Sign Company Plus 6 Options

21 Larry Albright Plasma Globes, Crackle Tubes and More
Subscribe

Bulletins
Get the most important news and business ideas from Signs of the Times magazine's news bulletin.
Most Popular
-
Tip Sheet1 week ago
Always Brand Yourself and Wear Fewer Hats — Two of April’s Sign Tips
-
Photo Gallery3 days ago
30 Snapshots of the 2024 ISA Sign Expo
-
Ask Signs of the Times5 days ago
Why Are Signs from Canva so Overloaded and Similar?
-
Real Deal2 weeks ago
A Woman Sign Company Owner Confronts a Sexist Wholesaler
-
Benchmarks1 week ago
6 Sports Venue Signs Deserving a Standing Ovation
-
Paula Fargo13 hours ago
5 Reasons to Sell a Sign Company Plus 6 Options
-
Photo Gallery14 hours ago
21 Larry Albright Plasma Globes, Crackle Tubes and More
-
Women in Signs2 weeks ago
2024 Women in Signs: Megan Bradley