News
Clearing the Air
The evolution to green paints is upon us.
Published
16 years agoon
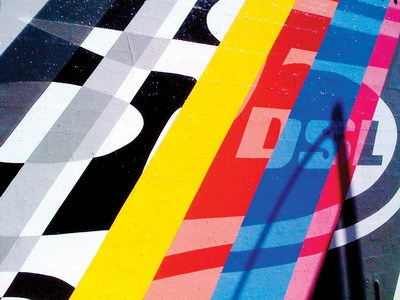
In these times of recordsetting petroleum costs, three “saves” rank high on everybody’s list: saving time, money and the environment. The paint and coatings industry has complied with these priorities by delivering improved environmental compatibility while retaining good application properties, at reasonable, or lower, costs.
National clean-air standards mandated environmentally friendly priorities, and the paint industry and chemical companies, after initial resistance, have seen “green” benefits – environmentally and fiscally. The initiative begat innovative solutions that filter through many industries. Waterborne products, in particular, reduce volatile organic compound (VOC) emissions while maintaining good performance. When technologies hybridize, we benefit.
Steve Shaklee, |1521|’s (Norcross, GA) specialty-coating product manager, worked in the sign industry 19 years and knows his company’s polyurethane-based product, Grip-Gard Plus, helps sign companies lower the amount of paint required for their paint applications, which limits VOC emissions.
Shaklee said, “Our products benefit well-trained signshops in that they’ll use less material and expend less labor. These are high-solids, low-VOC coatings that don’t rely on the addition of exempt solvents to achieve 3.5 lbs.-per gallon VOC levels. This higher efficiency benefits both the signshop’s bottom line and the environment.”
Shaklee hinted the company is looking to introduce a waterborne coating that’s been used for automotive applications.
AdvertisementMike Macre of |1561| (Chicago) said his company also focuses on products that reliably deliver what the sign industry needs, while meeting strict environmental standards. Spraylat’s Lacryl sign paints, used primarily on plastic sign faces, lower labor costs and boost sign longevity, compared to labor-intensive vinyl applications, according to the company website. Also, 1Shot lettering and bulletin enamels have long provided the gloss, applicability and durability needed for handpainted signs. All of the company’s products are lead-free.
Matthews Paint, a division of PPG Industries, places special emphasis on the signage industry. Donna Schaefer, Matthews’ marketing services specialist, said, “The company researches, develops and field tests products to bring our customers the most UV- and weather-resistant coating system available. Matthews’ coatings are environmentally safe and lead-free. Matthews manufactures VOC-compliant acrylic polyurethane coatings in gloss and satin, and meets EPA standards without sacrificing beauty or durability.”
Matthews is committed to the environment, Schaefer said, and “is continuously working toward being a more eco-friendly facility and coatings provider. Our facility is working hard to look at all aspects of our business, not just to meet today’s guidelines, but, where possible, to exceed them for the benefit of future generations of professionals.”
The chemical industry has gone “green” to help businesses offer sustainable products and services. The Environmental Protection Agency’s (EPA) Green Chemistry Program promotes innovative technologies that reduce or eliminate the use of hazardous substances in the design, manufacture and use of chemical products. Bayer Chemicals and PPG Industries have received the Presidential Green Chemistry Award.
Other pressures arise from the green-building scene. While they exert less pressure than clean-air initiatives, programs such as the U.S. Green Building Council’s Leadership in Energy and Environmental Design (LEED) rating system are pushing energy savings, resource conservation and indoor-air quality in the architectural-coatings sector.
More efficient and versatile equipment also contributes to green benefits. 3M introduced the 3M Paint Preparation System, which uses a wide variety of paints and eliminates the need for the traditional spraypaint-gun cups and filters.
AdvertisementThe evolution to green paints is upon us. Regardless of consumer, industrial or institutional paint categories, knowing how paint “works,” and applying the general “reduce, re-use and recycle” motto to shop practices, can save time, money and our planet.
Paint 101
Paint is a mixture of pigment and binder (the “glue” that forms a film that clings to the surface) that’s dispersed in a solvent. When the mixture is applied to a surface, the solvent evaporates, but the binder and pigment remain.
The paint-making process begins by mixing pigment with resin, solvents and additives to form a paste. Let’s examine the raw materials and their functions.
Pigments lend color. Solvents make paint easier to apply. Resins, or wetting agents, help it dry, and additives serve as fillers, binders and antifungicidal agents.
From hundreds of natural and synthetic pigments, titanium dioxide is typically selected for its concealing properties, and carbon black deepens the tint. Other pigments include iron oxide and cadmium sulfide for reds, metallic salts for yellows and oranges, and iron blue and chrome yellows for blues and greens.
AdvertisementNot bad, if you’re not eating them.
Extender pigments, which are also powdery materials, help control gloss and increase volume. Examples are clays, talcs and calcium carbonate. At this point, we’re still fairly green.
Binders must form smooth, durable, cleanable films easily at ambient temperatures, but typically accomplish this with solvents.
Solvents, which help paint dry, must dissolve film formers and make them into a usable liquid. Solvent choice determines evaporation rate, drying characteristics and viscosity, not to mention flexibility, strength and durability.
Typical binders include such natural or synthetic resins as acrylics, polyurethanes, polyesters, melamines, oils or latex. Modified oils called alkyd resins are the primary binders for oil- (or solvent-) based paints, because they dry harder and faster than natural oils such as linseed or tung oils. Acrylic or polyvinyl acetate are the primary binders for waterborne paints.
When such solvents as xylene, methyl ethyl ketone and toluene evaporate, they release VOCs. Fifty years ago, virtually all paint was solvent-based, but waterborne, or acrylic, formulations have largely replaced organic solvents in most paint applications in order to meet EPA and state/regional VOC regulations.
VOC emissions from solvent-based and, to a lesser extent, waterborne coatings release organic compounds into the atmosphere by evaporation after they’re applied. Though waterborne paints comprise mostly water, solvents that serve as coalescents to promote film formation still contain VOCs, but at a minimal level.
At this point, the sign industry hasn’t widely adopted waterborne paints because they haven’t adhered to rigid plastics and aluminum as well as polyurethanes. Macre said, “Most sign companies use solvent-based primers that, in certain areas, meet the local VOC limits. The two-part polyurethane topcoatings, depending on the area, also meet the VOC limits.”
Urethanes and polyurethanes
The terms “urethane” and “polyurethane” apply to certain types of binders used for paints and clearcoatings. In conventional paint, the film-forming component and pigment are deposited on the surface as the solvent evaporates. In urethane paint, however, the film is formed when an isocyanate, a family of highly reactive, low-molecular-weight chemicals, becomes a plastic-like substance. When there are two or more isocyanate groups on a molecule (diisocyanates or polyisocyanates), they can link with other molecules to form long-chained polymers called polyurethanes.
In one-component polyurethane paint, the isocyanate reacts with air moisture – the isocyanate is pre-polymerized (or already “reacted”), so very little isocyanate remains. In two-component paint, a moisture-curing chemical is added. The two-component system retains the hazardous isocyanate group. Once fully cured, polyurethane products don’t release isocyanates unless sufficiently heated by burning, welding and hot-wire cutting.
Overexposure to isocyanates leads to asthma and other lung problems, as well as irritation of the eyes, nose, throat and skin. Roughly one out of 20 people who work with isocyanates becomes “sensitized” to them, which means you could have an asthma attack any time you’re exposed to them.
Chemical companies have developed high-performance, waterborne, two-component polyurethane coatings that eliminate most, or all, organic solvents used in conventional polyurethane coatings. Waterborne polyurethane coatings reduce VOC and hazardous-air-particle emissions by 50 to 90%, companies claim, and replace them with water as the carrier, without significant performance reduction.
In order to bring two-component, waterborne, polyurethane coatings to the market, new waterborne and water-reducible resins were developed. To overcome some application difficulties, new mixing/spraying equipment was also brought to market.
Today, two-component, waterborne polyurethanes are being applied on industrial lines where fast-cure rates are required for such varied products as automotive coatings, metal containers and shelving, sporting equipment, metal- and fiberglass-reinforced utility poles, agricultural equipment and paper products.
Resin technology has improved waterborne paints’ adhesion, color retention, durability and flexibility, along with improved application characteristics. And don’t forget the easy cleanup.
Low- or zero-VOC paints
Although they contain little or no regulated VOCs, low- or zero-VOC paints contain acetone, ammonia, crystallizing silica and formaldehyde precursors. High-quality latex paint contains from 1 to 7% coalescing solvents per gallon, while low-odor (low-VOC paint’s other name, which emphasizes the readily apparent benefit) latex paints have less than 1% (these paints have soft, self-coalescing binders that don’t require much solvent).
Some low-VOC paints, however, don’t meet traditional, freeze-thaw standards. In cold climates, more care must be taken to preserve the paint, but technology is advancing in this area.
“Natural” paints, which are primarily manufactured by alternative paint companies, comprise such ingredients as plant oils (like citrus), plant dyes, natural minerals (clay, for example), milk protein and/or beeswax. These products often have longer drying times and still emit VOCs from turpenes or citrus oil.
Recycled paint is also an option for the green painter. Paint can be recycled by re-blending and reprocessing it. Recycling centers re-blend leftover paint by screening and remixing it, using few new materials. Reprocessed paint takes the same approach and mixes it with new materials, which allows a much wider color choice.
Reprocessed paint can be used for exterior painting, while the lower-quality re-blended paint should be used for interiors. Recycled materials can also be used in paint. For example, glass can be recycled into paint with some recycled paints containing up to 30% glass.
Eco-friendly removal
Manufacturers are developing safe, biodegradable paint removers that work quickly and effectively. However, defining what’s biodegradable, safe or speedy poses many challenges.
Most biodegradable paint strippers are based on one of the following chemicals: dibasic esters, N-methyl pyrrolidone, caustic soda, benzyl alcohol, hydrogen peroxide or sodium metasilicate. Traditional, non-biodegradable paint strippers are based primarily on methylene chloride, xylene and toulene.
Various brands may comprise any combination of biodegradable and non-biodegradable strippers. Some soy-based strippers break the molecular bond between the paint and the surface without melting or dissolving the coating. Other strippers based
on benzyl alcohol and hydrogen peroxide leave hardened paint chips.
Manufacturers of biodegradable strippers, which often dry at a slower pace than their caustic counterparts, say their products remove more paint in one application.
Equipment
Painting equipment impacts transfer efficiency, which measures how much paint makes it from the paint can to the surface.
Sign companies have benefited for years from high-volume, low-pressure (HVLP) sprayguns, which reduce overspray and improve transfer efficiency. However, 3M says its closed, filtered PPS system saves solvent use and gun-cleaning time, while improving operator efficiency.
The PPS system allows the use of the same pot for mixing and spraying. Paint is mixed in a disposable liner bag connected to a direct filter, which is mounted on a spraygun with a dedicated adaptor. When freshly filtered paint is dispensed, the liner bag collapses and allows the spraygun to work at any angle. Because the liner bag and filter are disposable, only the gun and adaptor need to be cleaned, which reduces the amount of solvent required.
Companies that wholesale aluminum or rigid-plastic signs should audit their paint-finishing systems, which, if done sloppily, can cost thousands of dollars in excessive costs.
A thorough audit identifies performance issues and operational costs by examining pretreatment-cleaning cost per square foot of product, overall first-pass yield, paint-finish defects, durability, specifications and curing/post-handling procedures, then evaluating corrective procedures, such as installing upgrade kits, changes in system cleaning and inspecting chemicals and paint from suppliers. A pre-treatment controller can significantly increase paint-finish consistency by automatically tracking and controlling operating parameters.
Shops that use paint booths should invest in a top-quality air-management system, which pays for itself quickly by increasing filter and fan life, lowering labor costs and minimizing energy usage, not to mention increasing paint-finish quality and containing VOC levels.
Recycle, reuse
The cheapest way to reduce pollution is to prevent it by reducing hazardous-waste generation, storage and disposal. Choose from various reuse and recycling methods:
Least effort: Contractors in your area who recycle solvent wastes pick up spent paint cans and solvents and replace them. When possible, reduce the number of different organic solvents used. This simplifies recycling. Often, one solvent can perform a job as well as two different ones.
Moderate effort: Set up a filtration system onsite to remove particular contaminants.
Most effort: If you use large volumes of paints and solvents, purchase or lease a still to recover them for reuse.
Here are some general tips:
• Use as much leftover paint as possible. Macre suggested mixing all the same types of products by manufacturer into a bucket and adding black paint. “Maybe you can get a slightly off-color black that can be used on the part of the sign that’s not seen.”
• Re-use spent solvents. Rinse equipment first with dirty solvents, followed by a small amount of virgin solvents.
• Keep inventory fresh by using the first-in, first-out system of usage. Label cans so you can tell when they’re purchased, Mike Koss, PPG Industries’ EHS manager, said.
• Eliminate “mystery” drums. Label drums and note the “in” date.
• Minimize color changes or paint with lighter color before darker ones to minimize equipment cleanouts.
• To dispose of paint scrapings, used paint filters, rags and other materials wetted or saturated with paint products that can spontaneously combust, thoroughly wet them with water and place them in a noncombustible container with a tight-fitting lid, or place them in a water-filled metal container, Koss said. Don’t dispose of them in regular waste containers. Rags soiled with hazardous waste should be collected and incinerated at a licensed waste-treatment facility, or possibly cleaned and returned for repeated use.
• Consult state and local EPA requirements for disposing rags contaminated with non-hazardous materials.
What’s next?
Development of newer, better-performing waterborne technology is leading the reformulation of solvent-based products. Paint manufacturers have also examined nanotechnology’s benefits.
This generation’s plastic, nanomaterials provide excellent abrasion resistance in automotive coatings and enhance color. Because they’re smaller than the wavelength of visible light (400 to 700nm), nanoparticles are clear, but diffract light to impart color – like a peacock feather. Other nano advantages include UV blocking, increased flexibility and stronger bonds.
PPG, which is participating in the EPA’s Nanoscale Materials Stewardship Program, offers a commercial, nanocomposite automotive clearcoat. Also, DuPont is pitching a family of viscous solids that can be sprayed and UV-cured to replace liquid coatings. Viscous solids don’t contain carriers or solvents – what applies is what dries.
Researchers have reportedly developed a low-cost, antimicrobial paint by embedding nanopar-ticles into vegetable-oil-based paints. The silver-embedded coating offers superior antibacterial protection to lengthen organic paint’s shelf life.
Chances are, painting facilities won’t switch from conventional formulations to nanotech in a nanosecond because they’ve tied up too much money in paint systems that currently serve their purposes quite nicely. However, remember this the next time you’re painting the walls in your house: The paint roller was lambasted when it was introduced because it dramatically increased productivity.
Regulations
Nearly every federal, state and local government that has regulated architectural and industrial maintenance (AIM) coatings (see sidebar on page 95) is considering further reductions. Several additional states are working on regulations as well.
The Clean Air Act of 1970 (with amendments in 1990 and 1997) authorized the establishment of National Ambient Air Quality Standards and requirements for state-implementation plans to achieve the standards. The EPA directs the establishment of national VOC-emission standards.
However, California set the stage for the national initiative. Low-VOC regulations began to take hold there in the 1980s, and the federal government followed by passing initial EPA VOC limits.
Subsequently, numerous states have enacted stricter limits (state and regional regulations can exceed, but not fall below, EPA standards). VOC recommendations developed by the California Air Resources Board (CARB) have served as a template for many states in New England and the Mid-Atlantic region. States in the Great Lakes region and the Midwest also are enacting stricter regulations, as did Canada in April 2008. Some states adopted Ozone Transport Commission (OTC) regulations.
Paint manufacturers won’t keep making boutique products for small markets. New formulations designed for California and the OTC are being applied across the board. So, even though, say Nevada, hasn’t signed on for state standards, manufacturers will sell the same paints there as sold elsewhere. From a supply-chain standpoint, it doesn’t make sense to offer multiple formulae.
Also, EPA regulations permit manufacturers to pay an “exceedence fee” in order to supply noncompliant specialty products. But that’s not allowed in the regions that have adopted new regulations. Sell-through provisions, however, allow distributors to sell inventory of affected coatings manufactured on or before the effective date.
Taking AIM
Architectural and industrial-maintenance (AIM) paints are used for decorative purposes, and as “commercial/industrial” paints that are primarily intended as structural protectants (paints for bridges, basecoats, primers, etc.). The California Air Resourse Board’s (CARB) website defines architectural coatings as “coatings applied to stationary structures or their appurtanances at the site of installation, to portable buildings at the site of installation, to pavements or to curbs. Appurtanances are accessories to an architectural structure, including, but not limited to: handrailings, cabinets, bathroom and kitchen fixtures, fences, decks, rain gutters and downspouts, window screens, lamp posts, signs, concrete forms, heating and air-conditioning equipment, large, fixed stationary tools and other mechanical equipment.”
However, lettering and bulletin enamels and metallic paints fall within the “Graphic Arts” category of architectural coatings (“coatings formulated and recommended for hand application by artists onsite using brush or roller techniques to indoor or outdoor signs [excluding structural components] and murals) and fall to the bottom of the hierarchy of paints that need to be regulated.
Jim Nyarady, manager of the Strategy Evaluation Section in the Stationary Source Div. of the Air Resources Board, said, “In general, if the paint is to be applied on a sign in the field, like a billboard, then it falls under local air districts’ architectural-coatings rules. The paint on the structure most likely would be classified as an ‘Industrial Maintenance,’ ‘Rust Preventative’ or ‘Nonflat’ coating. But the paints for the sign would be classified as a ‘Graphic Arts Architectural Coating.’”
If paints are applied to signs in a factory or a job shop, then rules other than those for architectural coatings (most likely, the local air district’s “Metal Parts” and “Products Coatings” or “Plastic Coatings” rules) apply.
In October 2007, CARB approved adding airbrush to its revised definition in its updated suggested control measure (SCM). The definition won’t be effective until a local-air district adopts the 2007 SCM, probably not until late 2008 or early 2009. When that happens, the effective date will be 2010.

SPONSORED VIDEO
Introducing the Sign Industry Podcast
The Sign Industry Podcast is a platform for every sign person out there — from the old-timers who bent neon and hand-lettered boats to those venturing into new technologies — we want to get their stories out for everyone to hear. Come join us and listen to stories, learn tricks or techniques, and get insights of what’s to come. We are the world’s second oldest profession. The folks who started the world’s oldest profession needed a sign.
You may like

Michigan Residents Make Parodies of Viral Detroit City Sign

What Makes the Perfect Sign Business Partnership

Marketing Signs to Schools, Tradeshow and Quote Follow-up Make May’s List
Subscribe

Bulletins
Get the most important news and business ideas from Signs of the Times magazine's news bulletin.
Most Popular
-
Photo Gallery1 week ago
30 Snapshots of the 2024 ISA Sign Expo
-
Ask Signs of the Times2 weeks ago
Why Are Signs from Canva so Overloaded and Similar?
-
Paula Fargo1 week ago
5 Reasons to Sell a Sign Company Plus 6 Options
-
Real Deal5 days ago
A Woman Sign Company Owner Confronts a Sexist Wholesaler
-
Photo Gallery1 week ago
21 Larry Albright Plasma Globes, Crackle Tubes and More
-
Women in Signs2 weeks ago
2024 Women in Signs: Brandi Pulliam Blanton
-
Women in Signs2 weeks ago
2024 Women in Signs: Alicia Brothers
-
Projects5 days ago
Graphics Turn an Eyesore Cooler Into a Showpiece Promo in Historic Plaza