Electric Signs
About Faces: A Long Look at Plastics
Tips on plastics usage, with some historical perspective
Published
18 years agoon
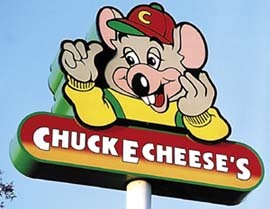
How do you select rigid plastics for sign faces? Does your supplier advise you what to use? Does your customer specify a plastic? How do you decide if the sign face will be flat or formed? Will the face be decorated with paint or vinyl, or will you, instead, opt for pigmented plastic?
There are many ways to answer these questions, but cost alone should not be the determining factor. Cost effectiveness should be. You should plan for your plastic-face sign to last at least 10 years. Anything less is a disservice to your customer.
The General Motors dealership-identification program from the early ’70s has used more acrylic than any other sign program over the ensuing 30+ years. Many signs have been up more than two decades and still look good. The program primarily has incorporated pigmented acrylic, mostly from Aristech (Florence, KY).
Very few electric-sign companies will get involved in a massive sign program like GM, but many of the particulars should be applicable for custom signage as well. In the midst of changing its corporate identity, Nissan is currently replacing formed faces with second-surface decoration.
First-surface decoration occurs on the outside of the sign, so it’s exposed to all of the elements. Second-surface decoration occurs inside the plastic face. While protected from the elements, it’s exposed to the lightsource that illuminates the sign (typically fluorescent).
All of Nissan’s and GM’s U.S. programs feature embossed signage, meaning the dimensional aspect is closer to the viewer. The opposite method, debossing, is more of an indention of the plastic surface. The face’s basic pan is embossed above the retainer level.
AdvertisementCopy is embossed above that level. Most signs have at least three levels of embossing:
1. The retainer level;
2. Top of the pan level; and
3. Top of the copy level.
In the GM program, the dealer name has always been produced by embossing a clear material, with second-surface painting.
Also in the ’70s, Cummings Signs (Nashville, TN) built the ARCO program, which identified the combination of four to five oil brands. All told, the program included more than 12,000 double-faced signs that averaged 55 sq. ft. (which means 1.3 million sq. ft. of acrylic material).
AdvertisementThis was the first national program to combine embossing with debossing on the same face. The word "ARCO" and the logo (known as "The Spark") were both debossed below the sign’s surface. The lettering and logo were pulled into the female cavity of the mold to form the debossed area. Cummings gave a 10-year warranty but never had a claim.
Besides acrylic, the only other choice was Uvex material (widely used today for protective eyeware), which is a cellulose acetate butyrate (CAB). This easy-to-form material accepted deeper draws. However, it didn’t weather well, especially compared to acrylic, which offers much better UV resistance.
Plastic hangups
All sign faces with rigid substrates should have some type of hanging bar for support. At a price of perhaps $2 per linear foot of sign face, it’s a great insurance policy. I suspect that dozens of warranty replacements could have been saved if all the faces were properly suspended on the signs.
Few installers want to accept the expense of the belt and suspenders approach (which isn’t cost prohibitive), but the key to hanging bars, strips and brackets is to securely hold the plastic from the top. The strips can be on the back, the front or even on top. If you use a belt and suspenders, put a strip on the front and back. I recommend this on any face more than 10 ft. tall.
There are many ways to attach these devices, but here are some common guidelines:
Advertisement* To ensure secure fastening, use screws, rivets or bolts. If you’re using double-stick tape, clean the surface carefully and add a few fasteners to the strip.
* Acrylics require more care than polycarbonates. However, they are more easily cemented.
* Provide a ledge or some other support for the sign. It can be a piece of sheetmetal bent to hold the strip. It also can be in sections, with spaces between suspension points. A 4-in.-long strip with 16 in. of space in between would be the maximum spacing. Continuous is always better.
* This hanging sandwich must have a tight fit. If you use a 1/8-in. hanging strip on a 1/8-in.-thick face, leave 1/2 in. of space between the inside of the retainer and the sign frame. Put a bolt, screw, rivet or some type of fastener at the top center of each face section.
Cracks in thousands of illuminated sign faces nationwide could have been avoided by spending an additional 1/10 of 1% for rivets for each job. They reduce the dirt and water that permeate the sign and prevent sign faces from riding up on each other, or breaking because of the unnecessary stress that the lack of rivets adds to the sign.
To install a double-faced, double-pole, 25-ft.-long (8 ft. tall in the middle) shopping-center sign, I bolted the faces to the sign and used a 3/4-in.-thick rubber grommet as a shock absorber.
I put my bolts on approximately 12-18-in. centers. I drilled an oversized 3/8-in. hole in the white pigmented acrylic and bolted it to the frame. The "V" configuration of the plastic face allowed for expansion and contraction, and the grommet’s rubber provided a heavenly cushion between the bolt and the plastic.
That sign is now at least 25 years old, and it has never had a crack between sections, a light leak nor a replacement face.
Thermoforming Tips
Information on thermoforming plastic is addressed elsewhere in this issue’s plastics coverage (see page 84). But here are some quick and easy tips:
* The thickness of the plastic can be reduced by using embossing. * It’s easier and faster to cut the masking on an embossed face.
* Properly applied paint, made specifically for this purpose, will last longer than any alternatives.
* Second-surface decoration is more reliable and longer lasting. * An embossed face is stronger and more wind resistant than a flat face.
* If you need 10 or more sets of faces at a time, prescreening is an option.
It seams to me
Seams between face sections are often problematic, because, done poorly, they can negatively affect crating, shipping, handling and installation. Butt seams simply don’t work because they don’t provide an overlap. A mitered butt seam provides a bit of an overlap due to mitering in opposite directions, but it’s still inadequate. A better method is a lapping butt seam.
To create one, first use a saw or router to cut half of the plastic’s thickness from two face sections. This forms the lap joint, or seam. Another method, which requires heat, only works with acrylic. The seam is created by bending one side of the plastic face 90° angle, and the flange is bent 90° to the first bend. Thus, a flange is created in the same plane as the first surface of the face. The two face sections are butted together, and the rear flange provides a great light barrier.
A new dimension
Today’s signmakers are fortunate to have many choices: modified acrylics, polyesters, polycarbonates, etc. There are advantages and disadvantages with all of these:
*Acrylics. They break the easiest of all four types, but they also offer the best weathering capabilities. Acrylics are naturally UV-resistant. With other plastics, this characteristic is either co-extruded as a cap layer or applied to one surface, usually by roller coating.
Acrylic is easy to vacuum form, but it can’t be cold-formed using a metal brake. Acrylics are stocked in the greatest variety of colors. A flat face of 0.125-in.-thick acrylic will stay more rigid in vertical planes than the other three types of plastic.
*Modified acrylics. These materials essentially possess all of acrylics’ characteristics. They are slightly less stiff than cell-cast acrylics, but their impact resistance exceeds acrylics’.
*Polycarbonate. Polycarbonate offers the best impact resistance. However, for UV resistance, a coating must be applied to the first surface.

SPONSORED VIDEO
Introducing the Sign Industry Podcast
The Sign Industry Podcast is a platform for every sign person out there — from the old-timers who bent neon and hand-lettered boats to those venturing into new technologies — we want to get their stories out for everyone to hear. Come join us and listen to stories, learn tricks or techniques, and get insights of what’s to come. We are the world’s second oldest profession. The folks who started the world’s oldest profession needed a sign.
You may like

Michigan Residents Make Parodies of Viral Detroit City Sign

What Makes the Perfect Sign Business Partnership

Marketing Signs to Schools, Tradeshow and Quote Follow-up Make May’s List
Subscribe

Bulletins
Get the most important news and business ideas from Signs of the Times magazine's news bulletin.
Most Popular
-
Photo Gallery2 weeks ago
30 Snapshots of the 2024 ISA Sign Expo
-
Ask Signs of the Times2 weeks ago
Why Are Signs from Canva so Overloaded and Similar?
-
Paula Fargo1 week ago
5 Reasons to Sell a Sign Company Plus 6 Options
-
Real Deal5 days ago
A Woman Sign Company Owner Confronts a Sexist Wholesaler
-
Photo Gallery1 week ago
21 Larry Albright Plasma Globes, Crackle Tubes and More
-
Women in Signs2 weeks ago
2024 Women in Signs: Brandi Pulliam Blanton
-
Women in Signs2 weeks ago
2024 Women in Signs: Alicia Brothers
-
Projects5 days ago
Graphics Turn an Eyesore Cooler Into a Showpiece Promo in Historic Plaza